In this article
How to Save 12 Weeks Downtime
Could your production line, or your entire operation, survive 12 weeks of downtime? It’s doubtful. But if one of your medium or high-voltage assets fails, that’s the kind of delay you could be looking at before you can get a replacement manufactured and back in action. So one day of Partial Discharge testing to avoid three months of lost production looks like a highly rewarding investment.
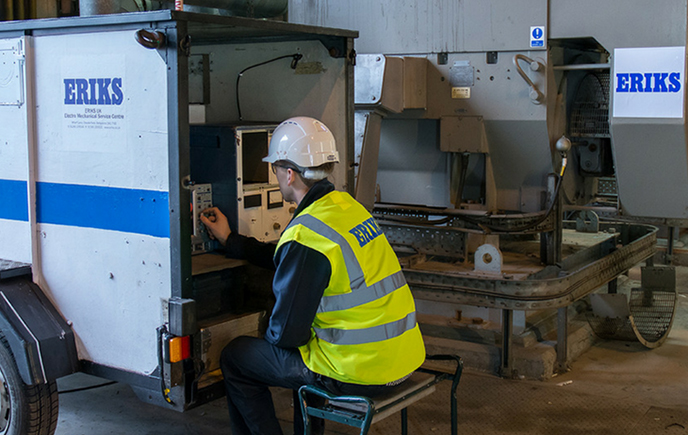
Partial Discharge (PD) testing is an effective method of measuring the “health” of a medium / high-voltage asset such as a motor, generator, transformer, switchgear or bus-bar. Repeating the tests regularly over time will determine the rate of deterioration of the winding, so you can assess the risk of failure and take steps to prepare, or undertake preventive maintenance or repair.
But what exactly is PD, how does it occur, and why should you worry about it?
Crossing the void
Partial Discharge is defined in IEC60270 as a “localised electrical discharge that only partially bridges the insulation between conductors” or on the surface of an insulation. There can also be surface PD as a result of conductive contamination by, for example, contaminated oil, dust, or water particles.
Partial Discharge occurs in all medium / high voltage rotating machines from the very first time they’re powered up. It can’t be avoided but it can be monitored. PD can also develop in static plant such as switchgear, bus-bars, transformers and cables. If monitored, it can be dealt with before it develops from a minor episode into a major problem.
The voids and gaps in a rotating machine’s insulation system which lead to PD, occur inevitably in the manufacturing process, which is why even new windings can be affected. And as time goes by, more voids and gaps can develop due to thermal deterioration, poorly-fitting coils, and coil movement resulting from looseness and vibration.
Although these causes of PD would be less of an issue on their own, they are compounded by the vicious circle of an increase in PD causing more erosion of the insulation, and erosion of the insulation leading to more PD. Leakage currents, travelling through the insulation to earth, can also occur for the same reason.
Ultimately, the resulting insulation decay, and the PD levels and leakage currents, will reach a critical point, and the insulation on the rotating machine, switchgear or transformer will fail completely – usually through a breakdown to ground. The good news is, unexpected failure and weeks of downtime can all be avoided, with ERIKS expert PD testing.
Testing, testing
Using a bespoke mobile test trailer and power transformer of the kind operated by ERIKS PD Testing service, it’s possible to carry out the test off line during a one-day shutdown. The results of an off-line test will give more in-depth information about the insulation system’s integrity, helping ERIKS to provide a more accurate assessment. In addition, if appropriate sensors such as Capacitive Couplers, Rogowski coils or RF CTs are installed in the machine, data can be monitored and analysed while the asset is on-line.
ERIKS are fully licensed to produce EXE-certified Rogowski coils and to install all the above on-line coupling devices. Please contact ERIK Chesterfield for more information.
Although actual time of failure can’t be predicted based on the PD test results, expert analysis can assess the risk so you can plan maintenance to prevent costly in-service failure. Repeating the tests at regular intervals can then determine rate of deterioration, to help build a better picture and provide a more accurate assessment.
While carrying out the PD Test to record electrical discharge, ERIKS can also undertake an additional offline test to measure Tan Delta (Loss Tangent), which represents the material and gaseous leakage losses. This further enhances the evaluation of the insulation system’s condition.
The dielectric loss tangent (Tan Delta) is affected by the void content of the insulation. The higher the void content, the higher the loss tangent. The loss tangent represents the sum of solid material (conductive type) losses and the gaseous losses as the voids within the insulation discharge, causing breakdown and ionisation.
Partial discharge in insulation systems is used to measure the magnitude of dielectric loss energy, often referred to as the DLA (Dielectric loss analysis) test. This represents the gaseous discharge losses within the voids. The DLA test has been superseded by modern Partial Discharge testing which provides more data to help analyse the condition of the asset.
The copper circuit of the winding of a rotating machine can also be tested – and its integrity evaluated – by ERIKS, using state-of-the-art surge comparison equipment and a low-reading ohmmeter.
Again, repeated testing will provide a range of results which can be trended to identify deterioration in insulation.
ERIKS provide a full technical report on each asset tested, with a comprehensive conclusion and recommendations. With the information at your fingertips, you can then take all necessary steps to prevent catastrophic failure and remove the risk of a lengthy period of downtime.
For more information on Engineering, Repair and Replace solutions please contact your local ERIKS Service Centre, who will be happy to discuss your options.
#ERIKS #LetsMakeIndustryWorkBetter #Engineering #RepairAndReplace #Investment #MaintenanceTesting