In this article
A fan-tastic result all round
When a fibreglass insulation manufacturer had a problem with a noisy fan unit, it wasn’t just risking catastrophic failure. It was also upsetting the neighbours. Fortunately, ERIKS’ know-how and ingenuity helped to keep the peace.
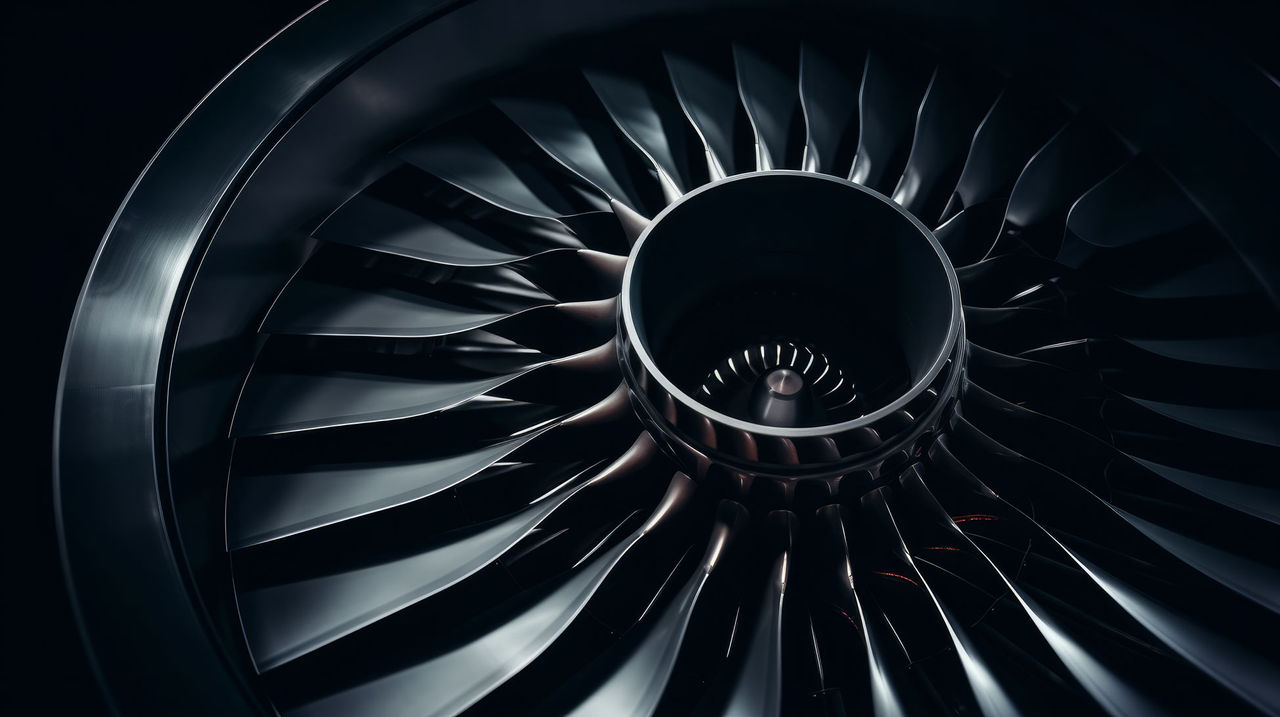
Maintenance engineers walk a tightrope between the pressures of production and the need to maintain assets at optimum efficiency. Often it’s the long-view which loses out, and a deteriorating asset is kept running until finally it falls over. Sometimes it brings associated assets down with it, but that’s a gamble with downtime that many manufacturers are prepared to take.
One customer’s critical fan unit was already on borrowed time, growing increasingly noisy and running hot.
ERIKS’ on-site team, which runs the customer’s engineering stores, advised keeping a spare unit ready in stock, until a suitable maintenance window could be found. Meanwhile ERIKS monitored the unit for vibration and temperature, to provide useful data ammunition for the maintenance engineers.
Talking hot air
The fan unit is vertically mounted on the outside of a chimney, which vents hot air from the manufacturing process. The fan extracts the air – loaded with tiny glass fibres – out of the chimney for filtering, so that only clean air is vented to the environment.
ERIKS’ Online Vibration Monitoring revealed a steady increase in fan vibration over several months, with two alarm levels breached. However the situation was confused when the bearing temperature – which monitoring revealed had also been rising – began falling again in.
Because the Online vibration data continued to show an upward trend, ERIKS’ engineers knew there must be another reason for the drop in temperature. And they found it was… a drop in temperature.
The customer’s site is in Scotland, and the cold Scottish winter weather had helped to cool the externally-mounted fan.
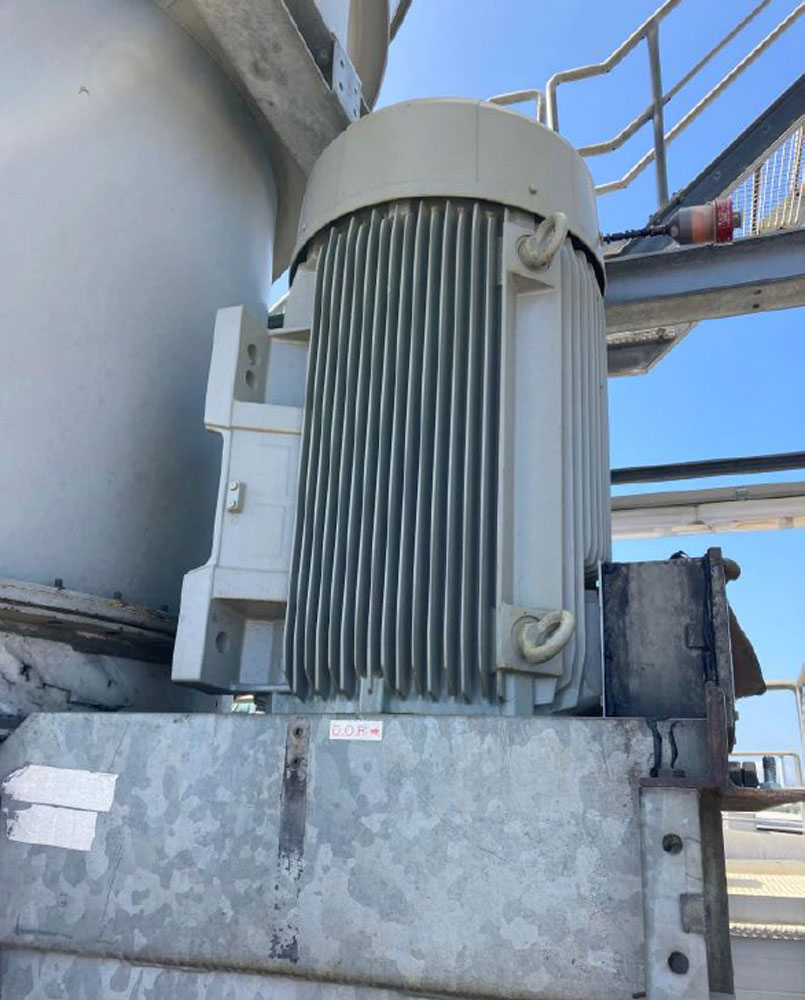
This anomaly shows the importance of having more than one set of data from more than one type of sensor.
With Online Vibration Monitoring still showing a rising trend, it was possible to confirm that the problem remained, and the root cause was still unresolved.
Now the customer’s own maintenance engineers had a valuable counterbalance to the production department’s demands, and a brief shutdown was quickly arranged.
A race against erosion
With the fan’s metre-high motor removed from the chimney and taken to ERIKS’ local engineering workshop, it didn’t take long to discover the cause of the vibration and rising operating temperature & noise.
The outer bearing race was showing clear signs of erosion due to electrical fluting. The rotor of the inverter-driven motor was generating an electrical field, and the current was escaping via the bearing. Every time it did, it created a tiny electrical arc which was gradually eroding the bearing metal.
Undetected and unresolved, the bearing deterioration could have catastrophically affected the motor, fan, pulleys and drive belt. In the worst-case scenario even the chimney stack could have been damaged, and a fire could have resulted.
To prevent a repeat of the problem, ERIKS fitted a bearing with an insulated outer race. This reduces the amount of current passing through the bearing and minimises the resulting electrical fluting. In addition, earthing brushes were fixed to the body of the motor, to provide contact with the exposed shaft at the drive end. These brushes offer an easier route for the current to escape to earth.
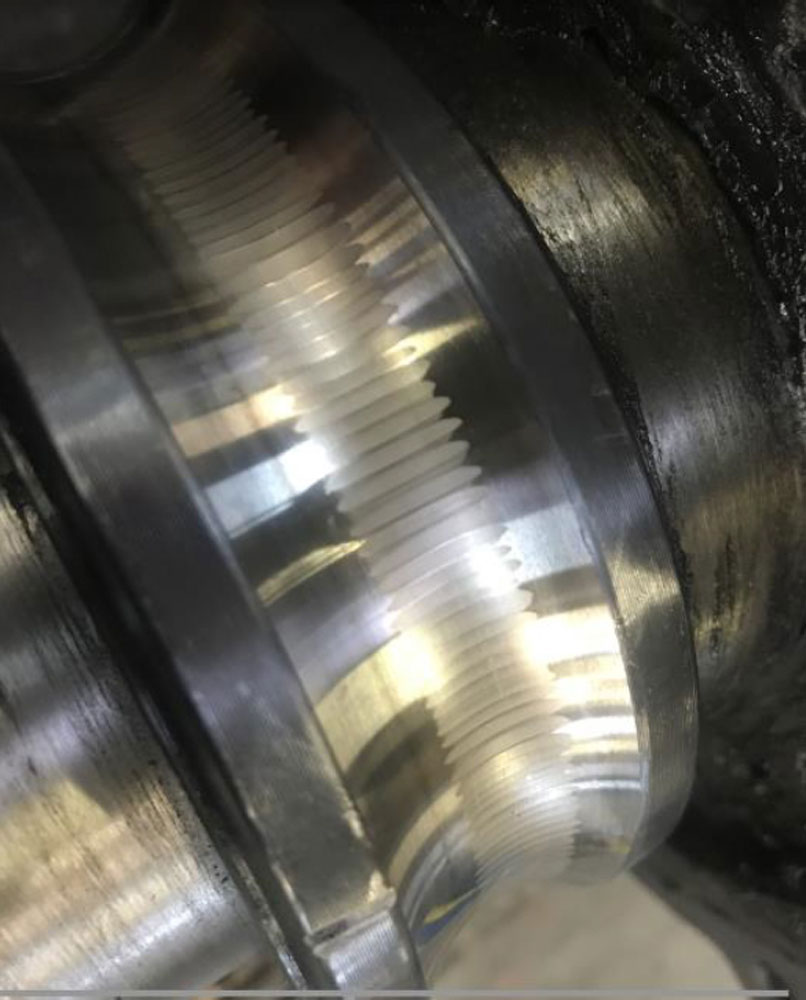
Readings from sensors fitted to the new motor show that both vibration and temperature have been dramatically reduced. Meanwhile the overhauled and updated motor remains in the engineering stores as a spare.
To prevent a repeat of the problem, ERIKS fitted a bearing with an insulated outer race. This reduces the amount of current passing through the bearing and minimises the resulting electrical fluting. In addition, earthing brushes were fixed to the body of the motor, to provide contact with the exposed shaft at the drive end. These brushes offer an easier route for the current to escape to earth.
Readings from sensors fitted to the new motor show that both vibration and temperature have been dramatically reduced. Meanwhile the overhauled and updated motor remains in the engineering stores as a spare.
Music to their ears
It wasn’t only production which was threatened by the problem with the fan. The noise from the increased vibration – the result of the electrical fluting – was also attracting complaints from nearby residents.
Before ERIKS’ intervention, the customer had been planning to spend around £40,000 on an acoustic chamber for the motor, to muffle the noise. The new and improved motor has proved so much quieter that complaints have stopped and the idea of the chamber has been scrapped.
Good relations with the neighbours – and £40,000 – have both been saved.
For more information on ERIKS' Vibration Monitoring or Engineering solutions and to get in touch with one of our Engineering Specialists please contact your local ERIKS Service Centre, who will be happy to discuss your options.
#ERIKS #LetsMakeIndustryWorkBetter #VibraConnect #OnlineVibrationMonitoring