In this article
Saving energy for customers is our bag
Helping customers maintain and repair their assets, to minimise downtime and maximise productivity, are our key concerns. But if we can optimise efficiency and reduce energy use at the same time, so much the better.
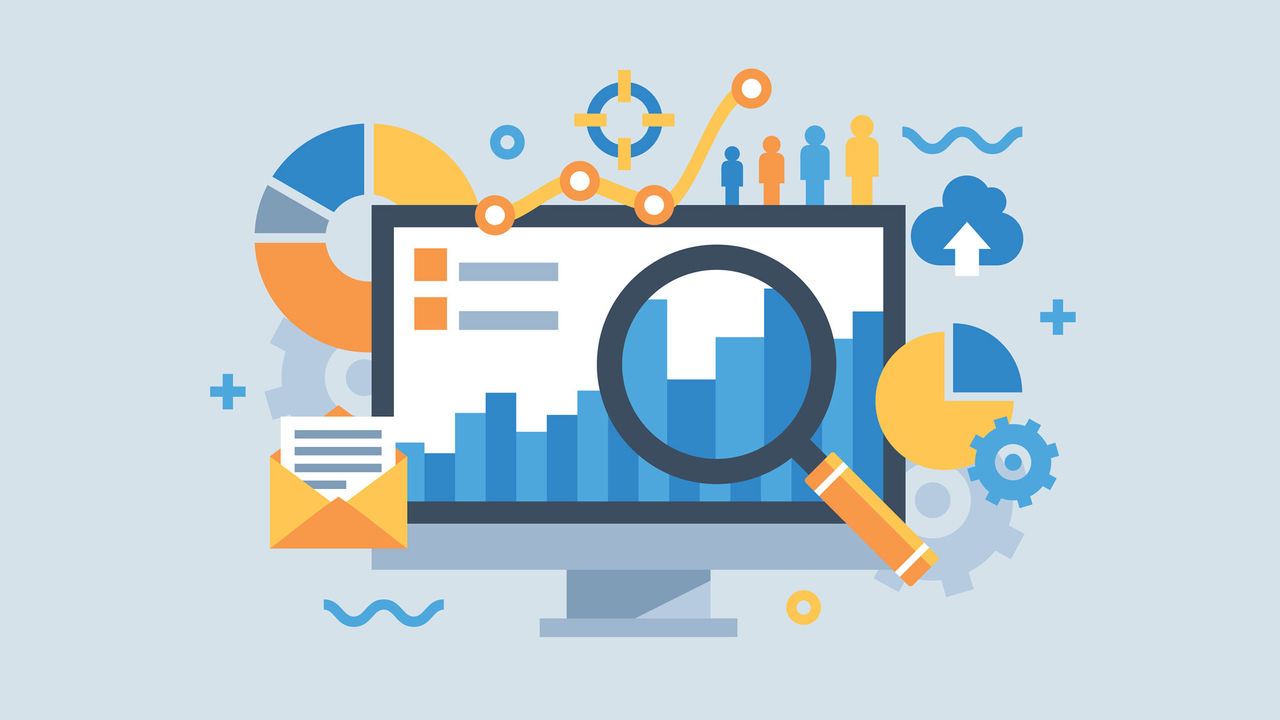
The UK’s leading paper bag manufacturer was having issues with a slip ring motor on one of its production lines. Over 70 years since the line was first installed, replacement parts are no longer available as a standard order. So bringing the machine’s complex design back to spec would need more than a paper bagful of cash. The estimate was around £38,500 in total.
This is where ERIKS’ repair / replace neutrality comes into its own – enabling customers to make informed decisions that are right for themselves.
With ERIKS’ impartial advice, the customer decided a new motor and drive system would be a more cost-effective option than repair. And that ERIKS would be the best people to provide it.
Working in the dark
While the customer’s own on-site team worked on upgrading the mechanical components, ERIKS began work on the installation of the motor, powertrain, new electrics and the automation systems.
The line’s age meant that the original engineering drawings had long since disappeared. And after several decades of on-the-hoof repairs and undocumented upgrades, even if they had been available they wouldn’t have had much resemblance to the asset that confronted today’s engineers.
So as the installation proceeded, several unexpected issues were revealed and challenges were overcome. However the outcome was the development of a far more refined solution for the new main drive panel, with a number of improvements and benefits.
Looking good on paper (bags)
Productivity and performance are important. Safety paramount, that’s why ERIKS recommended the installation of a new Pilz safety PLC for the main control panel. The safety design is certified to the highest possible level for the customer’s complete peace of mind.
The new print station motor is now controlled by an inverter, which is more effective at protecting the station’s mechanical components. In addition to a soft-start and soft-stop function, in the event of a printing jam the inverter will trip far faster than the original direct-on-line system – helping to reduce the likelihood of serious damage to the print mechanics.
The rubber roller is particularly at risk if the machine is stopped and the roller is left in contact with the print plate.
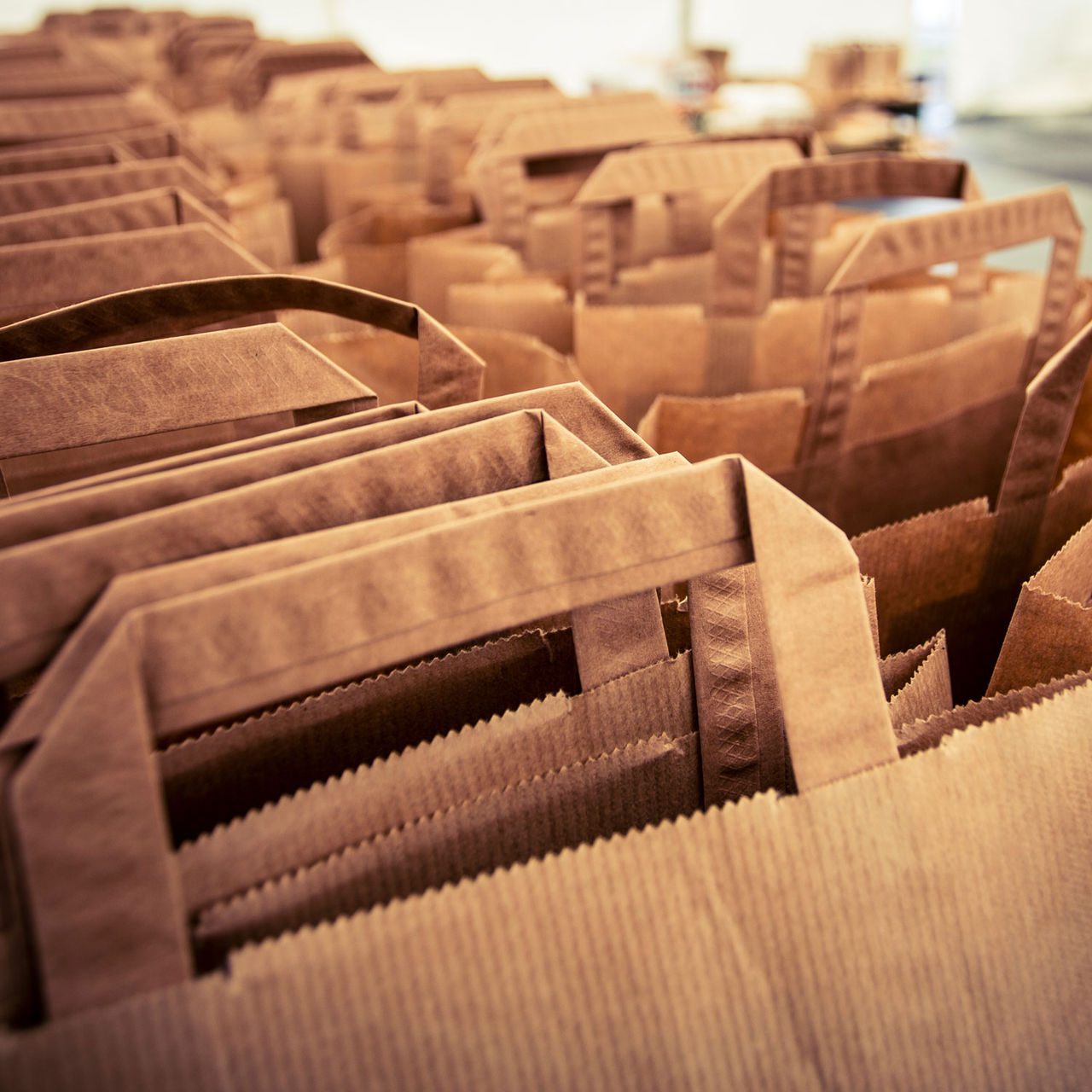
This can cause an irreparable dent in the rubber which means the roller has to be scrapped. The automatic mode for the print station makes this much less likely to happen.
Making a good impression
The print station drive now operates independently of the main drive. Once the print impression function has been turned on, the independent drive can be set to auto control.
Then, if the e-stop, safety guard, web brake or main drive stop is activated, the impression will be turned off and the print roller will automatically disengage. This not only protects the roller from damage, but also protects the customer from expensive roller replacement costs.
And that’s not the only saving ERIKS achieved for the customer.
Saving energy, night and day
The WEG IE3 motor, Fenner drive and Fenner pulleys proposed and installed by ERIKS are delivering significant energy cost savings.
Operating both day and night shifts, the customer is charged a slightly lower rate for electricity used overnight. So the greater energy efficiency of the upgraded machine is saving £4,500p.a. on night-time energy costs, and £6,000p.a. on daytime energy bills.
As a result, the upgrade will pay for itself in just 3 years through energy savings alone. And as these two quotes prove, it doesn’t stop there.
The first quote is from the customer, who says that ‘it was a great job and the machine has been running very well since. We… really appreciate the great service and partnership which is developing between our respective companies.’
The second quote is the kind you’d expect from ERIKS, detailing the cost of a similar upgrade on another of the customer’s paper bag lines.
Once approved, it looks like more energy savings are in the bag.
For more information on Power Transmission or Electronics Repair and Replace and to get in touch with one of our ERIKS Specialists, please contact your local ERIKS Service Centre, who will be happy to discuss your options.
#WEG #Fenner #ERIKS #LetsMakeIndustryWorkBetter #Motors #EnergySavings #CostSavings