In this article
Stop recurring problems in their tracks
Reduced maintenance through increased insight
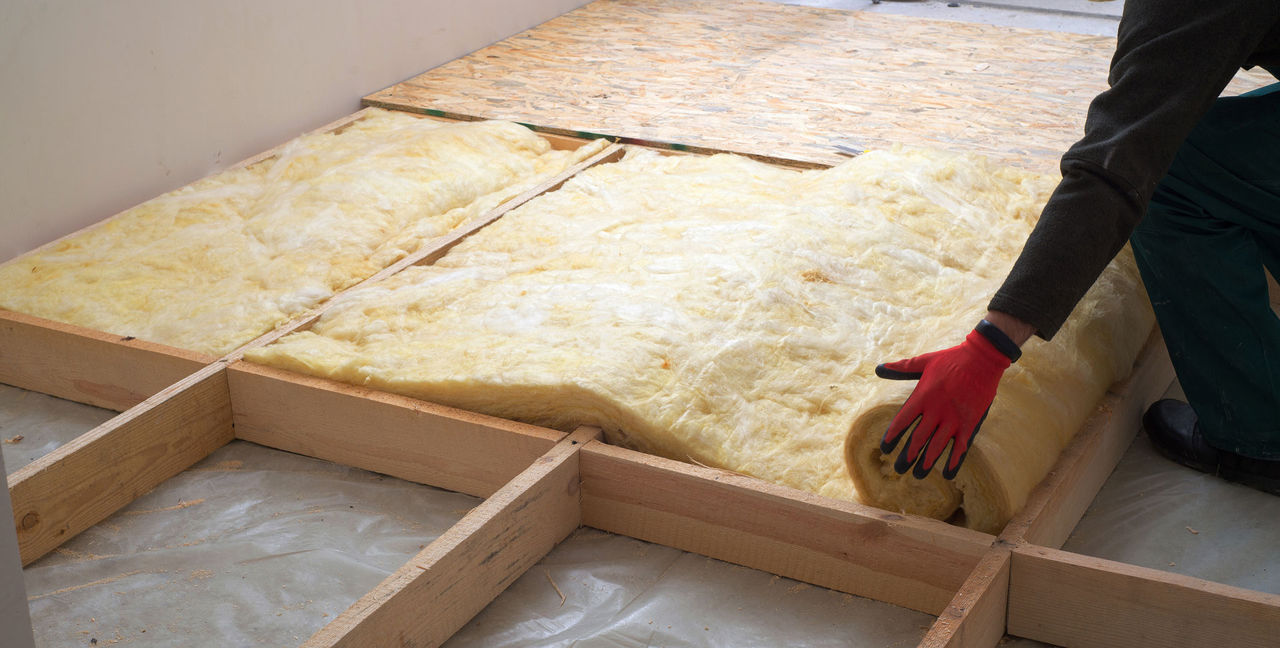
Industry Sector:
Construction / Insulation Manufacturing
Application:
White Wool Transport Fan Drive Motor
Actual Saving:
£56,000 (cost avoidance)
Payback period:
2 days
Product/Service:
- Digital Reliability Services
- Online & Reliability Monitoring
- Engineering Services
Customer Benefits:
- Reduced maintenance
- Increased MTBF
- Future foresight and insight
- Condition-based maintenance
For an engineer, what’s worse than an asset failure? Repeated failures of the same asset. But what’s even more frustrating, is repeated asset failures with no explanation.
Failures of any sort only have negative consequences, whether that be increased downtime, lost production, excessive maintenance, they all lead to one thing… avoidable cost losses.
With the complexity of today’s machinery, the importance of having foresight into the condition of your assets is now more important than ever. Just imagine the positive effects of foreseeing production issues before they become catastrophic.
For one independent insulation manufacturer, who was experiencing regular failures on a fan drive motor, investing in ERIKS Digital Reliability Services provided the answers to one of their long-standing questions.
Challenge
The white wool transport fan drive motor in question had clearly experienced significant, undetected deterioration, and failure of the motor non-drive end bearing had been reported on three occasions over the previous 18-month period. That’s an average Mean Time Between Failure (MTBF) of a lowly six months. Troublesome to say to least.
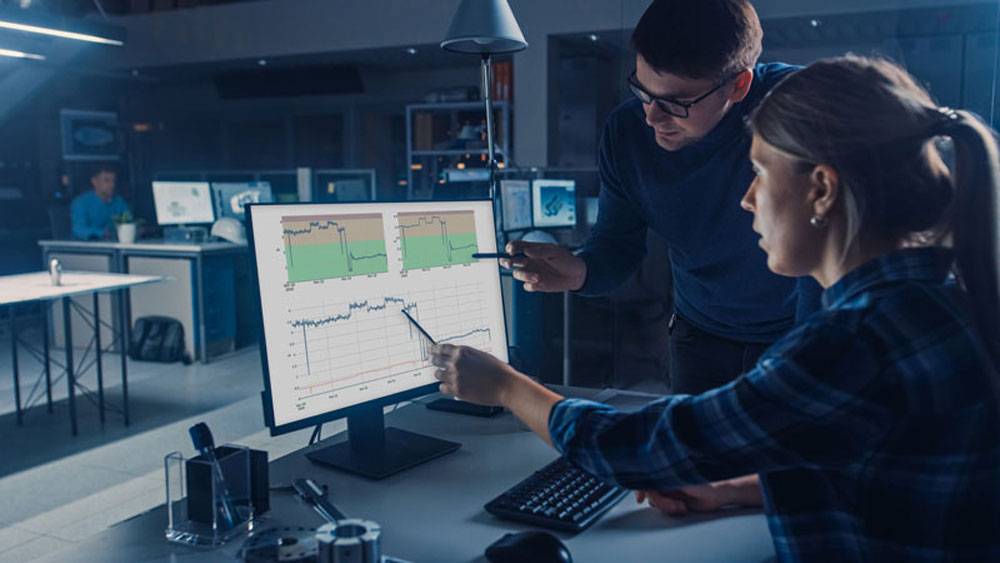
Data trend analysis on ERIKS SAM platform
Following the installation of ERIKS Digital Reliability Services online monitoring which includes tri-axis accelerometers logging velocity, acceleration and temperature, trend data over a five-month period highlighted that acceleration peak and rms amplitudes were steadily increasing and breached agreed warning thresholds.
It was estimated that the bearing would reach critical levels within just a matter of weeks. And the last thing that the customer needed was another catastrophic failure that could have a serious knock-on effect to production.
Solution
ERIKS Condition Monitoring specialists analysed the data, and following an extensive investigation, it was confirmed that the NDE bearing was the main reason for the deterioration, due to electrical fluting, and the root cause behind the impending failure.
Upon dismantling and inspection of the drive, it was noted that the whole drive was mounted on anti-vibration mounts, which were acting as an insulator to the earth bonding methods that had been installed. In addition, the bearing was being affected by the harmonics and eddy currents from the inverter, which was most likely the cause of repeat failures and deterioration.
It was also found that bearing grease had a blackened appearance, most likely caused by electrical arcing and exposure to current, while the NDE bearing housing showed evidence of excessive clearance and wear on the lower half.
Taking the application out of service would have seriously hindered the customer's production, so the decision was made to switch out the NDE bearing in-situ and make a few essential changes to increase the performance and reliability.
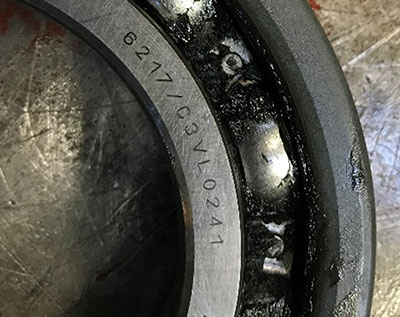
Bearing displaying signs of contaminated lubricant
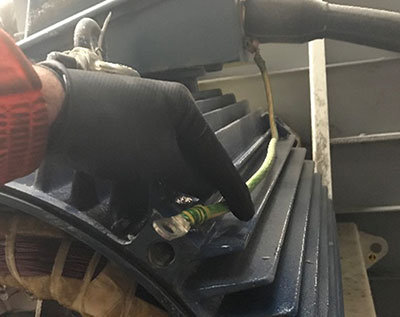
Remedial engineering work on NDE drive motor
A harmonic filter was fitted to the inverter to help protect the bearing, separate earthing of the main drive motor, and an AEGIS shaft grounding ring were also introduced to eliminate electrical arcing.
Result
Since undertaking the remedial engineering work, changing out the bearing, and returning the application back into service, the data has displayed a significant drop in acceleration peak. The data has also reported the period where the grease came up to temperature and stabilised, proving extremely valuable for future trending and analysis.
Installing this particular asset with ERIKS online monitoring wireless sensors has allowed the customer to progress closer to their desired condition-based maintenance (CBM) strategy.
Moving forward, the ERIKS Digital Reliability Services dashboard will allow the customer to gain a better insight into the health of their critical assets, receiving alerts should pre-determined thresholds be triggered, while real-time data allows for in-depth trend analysis over time periods, assisting them in discovering any similar or recurring problems.