In this article
OPTIME is on your side
Every maintenance engineer can agree that a clearly defined maintenance regime is essential. Especially in harsh industrial environments such as mining, raw material processing, paper and cement production. But a time-based regime is not always the best solution. Condition-based maintenance – of the kind made possible by Schaeffler’s OPTIME and other solutions – can be far more cost-effective.
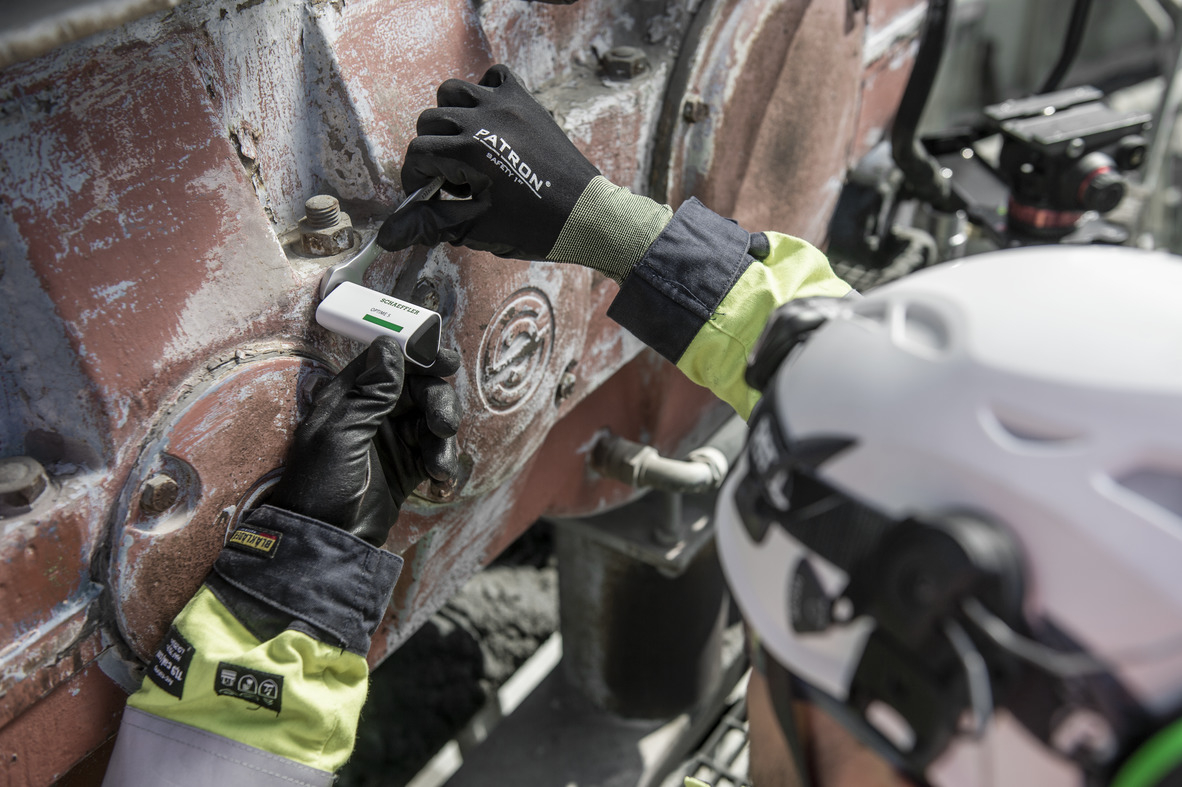
Taking a component offline for maintenance at set periods inevitably means an equipment shutdown – even when there’s no immediate need for maintenance to be carried out. It also fails to eliminate the risk of machine failure, as components may deteriorate between scheduled maintenance intervals.
However, a lifetime solution such as Schaeffler’s OPTIME transforms asset maintenance, by adding intelligence to sensors.
Monitoring and assessing the performance, quality, efficiency and status of machinery is the foundation of condition-based maintenance. As components wear, vibration increases until it reaches a threshold that triggers an automatic alert and prompts further investigation regardless of any rigid maintenance schedule – which might come into play too soon. Or too late.
Modern condition monitoring systems are designed with harsh environments in mind, where sensitive electronics have traditionally struggled. This enables an almost immediate return on investment.
ROI ASAP
In paper production, extreme humidity and high operating temperatures, coupled with demand for ever-increasing operating speeds, make longer bearing service life vital. Rolling bearings in this environment must withstand shaft deflections, moisture and extreme temperatures, to ensure dependable operation.
A leading global provider of renewable solutions in packaging, biomaterials and paper was experiencing ongoing issues with rolling bearings. Even so they felt the cost of implementing a condition monitoring solution was prohibitive – until the low capital expenditure associated with Schaeffler’s OPTIME changed their mind.
Within the first few months of implementing the condition-based monitoring system, their decision proved right. OPTIME indicated problems in no fewer than 16 machines: enabling early intervention and significant savings on downtime, lost production and repair costs.
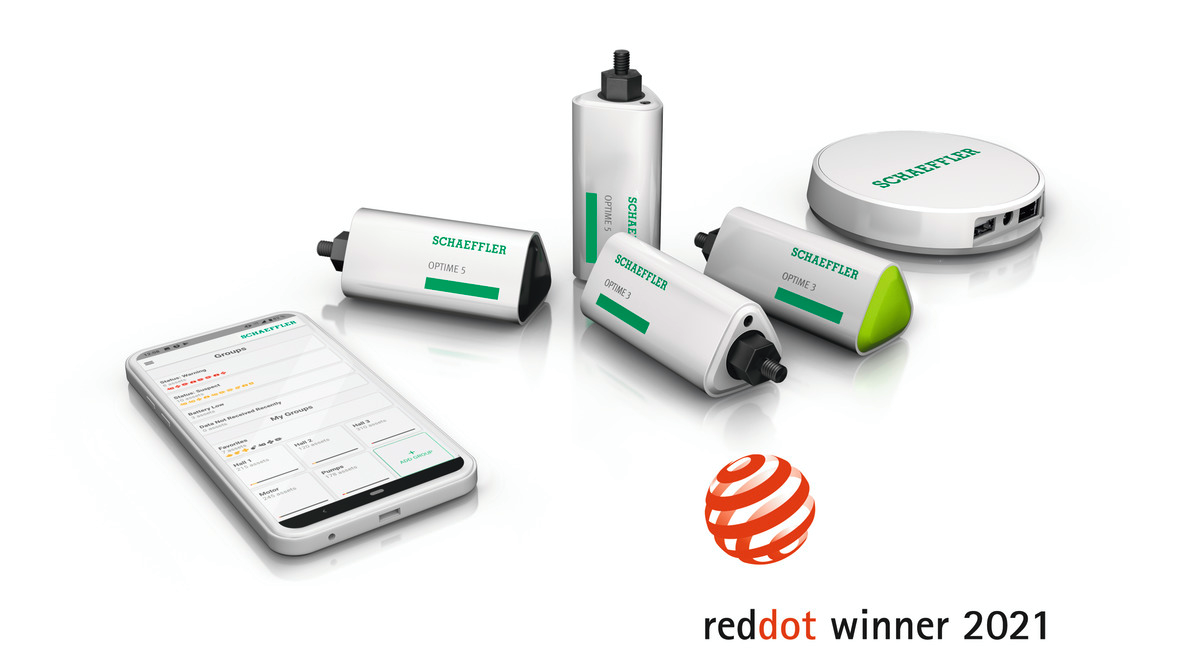
A further development to OPTIME is the development of OPTIME C1. Proper lubrication is the key to prevention, and here for example, 80% of rolling bearing premature failures could be prevented, thus providing maintenance crews with key information on all networked lubricators. This enables targeted maintenance of relubrication systems for optimum lubrication efficiency.
Seeing the bigger picture
The cost of condition monitoring solutions will usually be offset by the prevention of consequential damage. Though the success of an installation depends on how well it is tailored to the customer’s requirement.
In the steel and metalwork sector, rolling bearings can be affected by high temperatures, high speeds, and excessive exposure to contamination and water. The sector also relies on a wide range of unique equipment, including hot and cold rolling mills, coating units, straightening machines, casting plants, wire mills and converters. This is where a condition monitoring solution such as Schaeffler’s ProLink multi-channel system comes into its own.
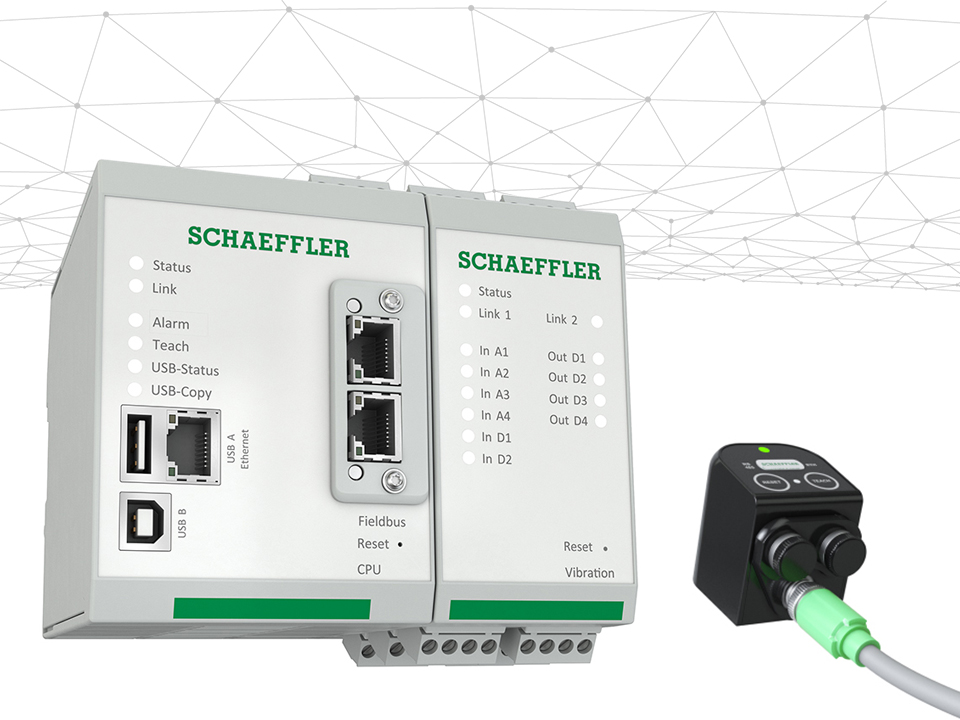
For example, ProLink can monitor the condition of a wire mill finishing block through vibration measurement – offering versatile options for easy integration and distribution of measured data.
To ensure rolling bearings and gear teeth are precisely monitored, a load proportional signal can be evaluated for every gearbox. ProLink also ensures a high level of transparency, and its modular, scalable design makes it highly flexible.
SmartCheck is another Schaeffler solution, ideal for when continuous decentralised monitoring of machinery and process parameters is required. Compact, innovative and modular, it can be used on assemblies where monitoring was previously considered too costly.
Condition-based maintenance solutions of the kind Schaeffler offers are at the heart of Industry 4.0. By providing all the information required for accurately visualising a machine’s operating status, they can enable more effective business decision-making, save money, and improve production efficiency.
Even in the most harsh and extreme operating conditions – from raw material extraction and processing, to paper production and pulping or cement production – Schaeffler’s condition monitoring solutions get going when the going gets tough.
90 machine failures v 150 sensors
A manufacturer of raw materials including cement, concrete and lime was experiencing around 90 machine failures every year. This had a significant impact on machine uptime, productivity, and maintenance costs. Schaeffler installed 150 wireless sensors connected to the OPTIME solution, to monitor the customer’s motors, fans, pumps, and gearboxes on a largely automated and permanent basis. The resulting data are now analysed to diagnose equipment issues, enable the factoring-in of personnel requirements, and to ensure timely procurement of replacement parts.
For more information on Condition Montoring, contact your local ERIKS Service Centre, who will be happy to discuss your options.
#Schaeffler #ERIKS #LetsMakeIndustryWorkBetter #OPTIME #ConditionMonitoring #Maintenance #Solutions