In this article
An end to production line hold-ups
Bearing replacement helps cut down time
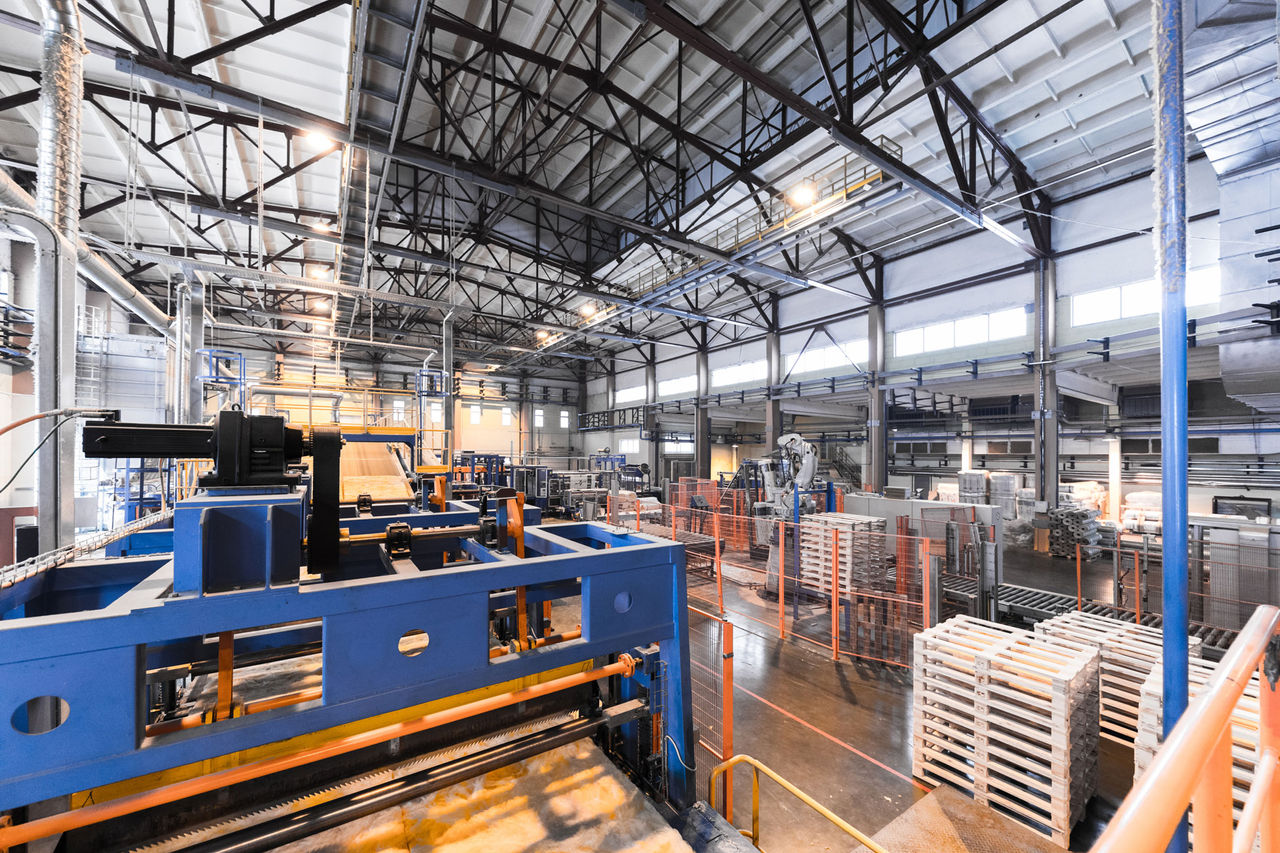
Industry Sector:
Primary Industries
Application:
Forming conveyor
Actual Saving:
£72,000
Payback period:
4 Weeks
Product/Service:
- System inspection and upgrade
- Filter supply and installation
- Training and knowledge transfer
Customer Benefits:
- System improvement
- Reduced maintenance
- Increased productivity
- Improved relability
Downtime resulting from equipment failure not only disrupts production but costs money and wastes time and materials. In one case, the failure of something as simple as a bearing led to a solution that took an initial full-day downtime and slashed it by 85% to save the customer £72,000.
Challenge
The customer is a large manufacturer of glass wool for insulation. The product starts out as dry materials, including recycled glass, cullet, and sand, which is heated until it melts, and spun like candy floss to form glass wool.
The final stage is a forming conveyor which forms the glass wool into sheets which can then be rolled to form the final insulation product.
The roller bearing on the forming conveyor used to fail every six months, taking over twelve hours to change, and requiring an external team to come in with cranes, hoists, and slings to remove the heavy bearing and the shaft, and replace with a new bearing.
The forming conveyor was shut down and completely removed from the production process during removal and reinstallation, but the melting process could not be stopped, creating a backlog of material to be stored and fed back into the process once the forming conveyor was back in service.
The cost to production of shutting down the conveyor was significant - £7,200 for each hour of downtime — meaning a 12 hour shutdown would cost over £86,000 every six months.
Solution
ERIKS got together with Timken to review the problem and, working closely with the customer's on-site engineers, came up with a solution: an SNQ diagonal split bearing which would make replacement much simpler and would reduce downtime by almost 85%, from twelve hours to two.
Thanks to it’s design the SNQ can be split and separated around the shaft. By removing the support cap and the top half of the housing all internal bearing components become visible and accessible making repairs and maintenance much more efficient and easier.
Timken offer eight seal variations for their SNQ, and this particular configuration was supplied with the Kevlar packing seal: a highly effective seal in fine particle environments. It offers a barrier for the bearing against penetrative contaminants, making it the perfect choice against this environments glass dust and powdery fibreglass shards.
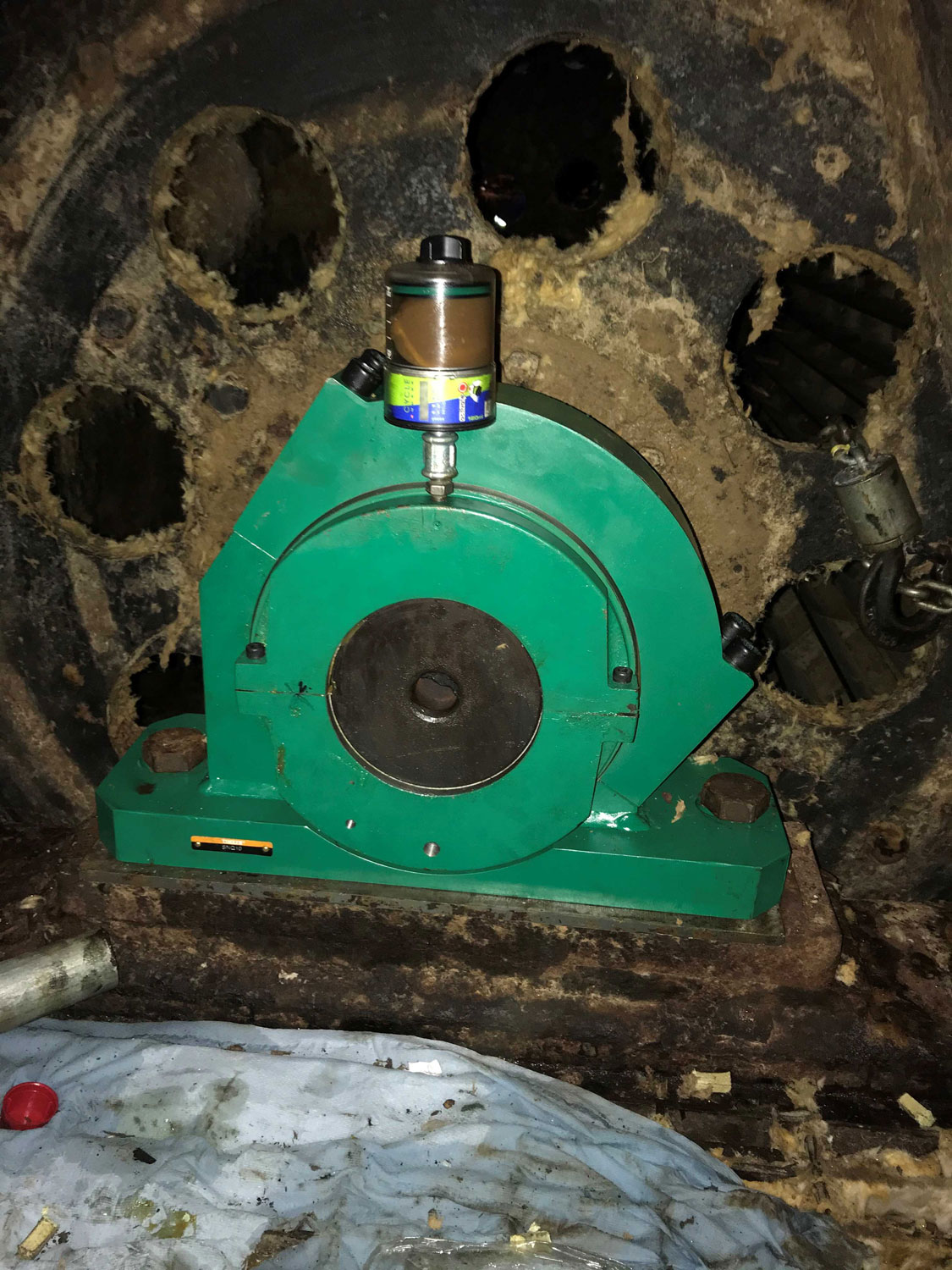
SNQ Diagonal Split Bearing in-situ
Result
Once in situ, the customer needed to be sure that the bearing would do what it needed to do, so the initial six month trial was extended to twelve months. A year later, the bearing is still in service and showing no signs of failing.
If and when the bearing does need repairing or replacing, downtime is slashed from the previous twelve hours to just two hours — saving £72,000 in lost production, not to mention the need to call in outside specialists. With appropriate training, the customer’s own on-site engineers can handle the repair.
A maintenance programme was agreed, and the customer was advised by ERIKS to keep spare parts for the bearing in their stores so future repairs can be handled onsite and with the minimum amount of disruption.
Thanks to collaborative working between ERIKS, the manufacturer and customer, production at the plant is much more stable and predictable.
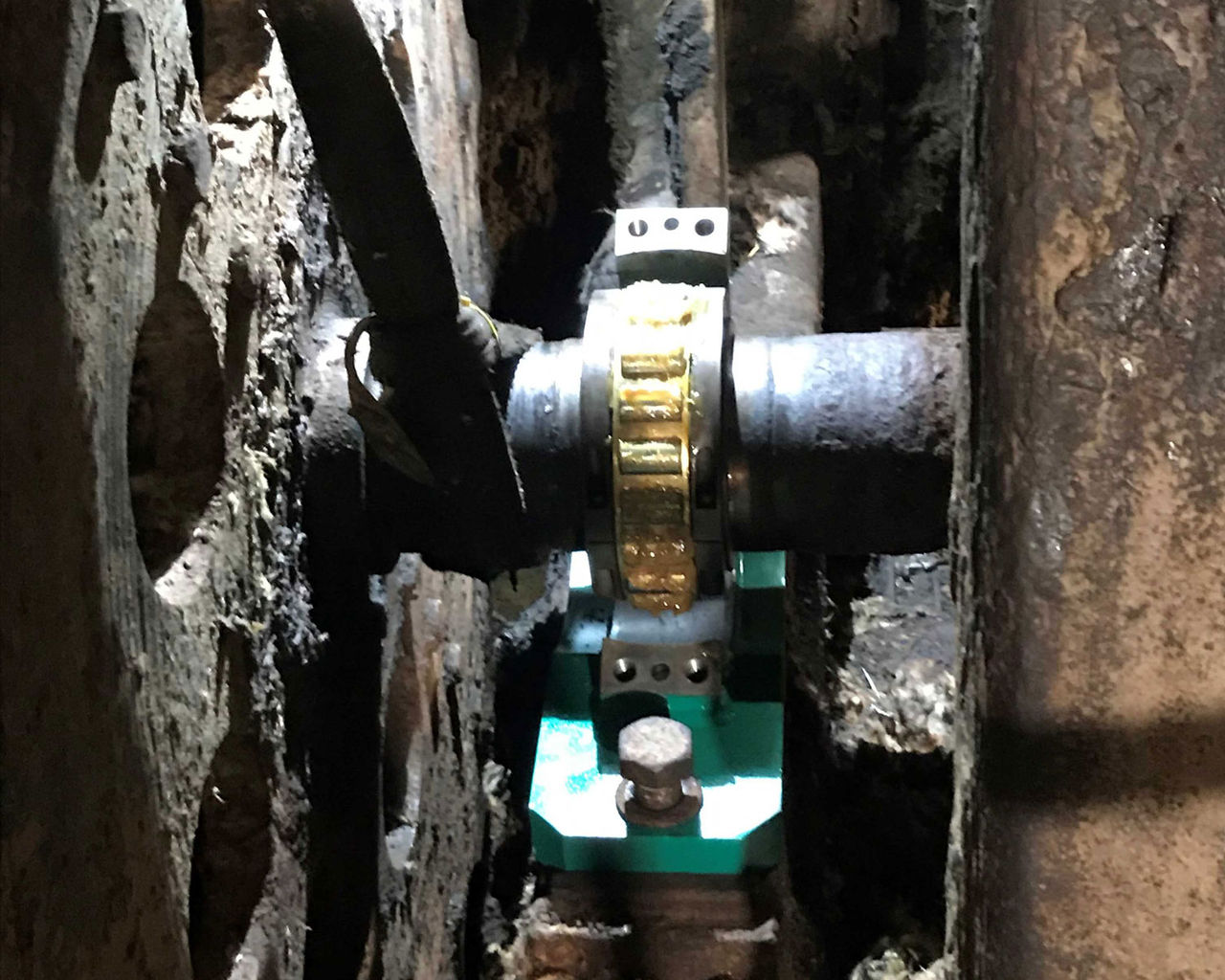