In this article
When pump efficiency is a sticking point
In the paper industry. In power generation. Across the chemicals, mining, oil, gas, and even sugar sectors. Anyone responsible for asset maintenance in a processing operation knows just how production-critical a pump can be. So proactive pump maintenance using innovative solutions can make the difference between efficient productivity and unplanned downtime and lost output.
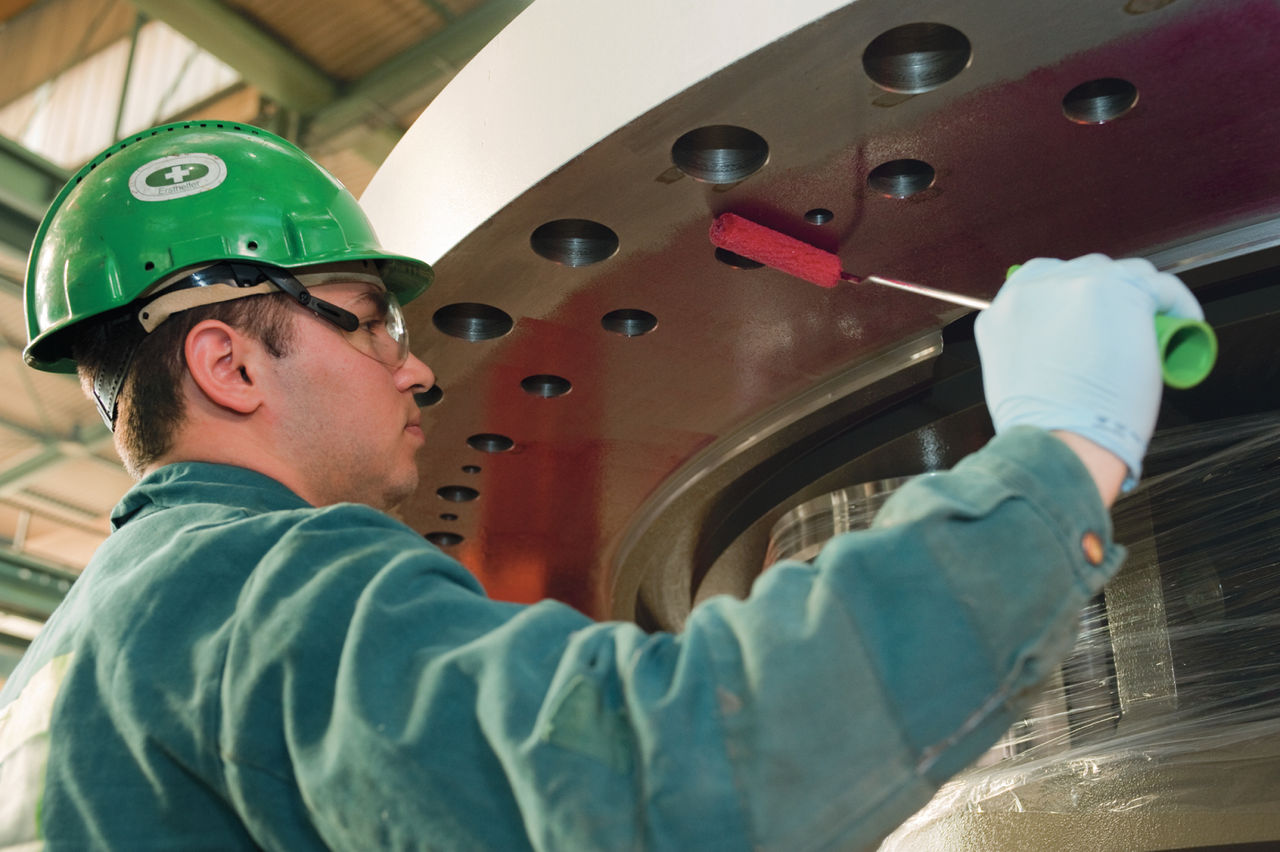
One such solution to eliminate common failure modes and extend the useful life of pumps is a liquid gasketing adhesive like LOCTITE® 518. Conventional pre-cut compression gaskets may shrink, relax, extrude or simply break – any of which will allow leakage between the bearing frame and adapter or stuffing box and pump casing. A liquid gasketing adhesive, on the other hand, fills all the air space between the mating parts, to create the perfect seal. And it has the added benefit of simultaneously eliminating flange face corrosion.
LOCTITE® 518 is a methacrylate-based gasketing product which not only optimises the reliability of the seal, but also speeds up repair due to its low strength and easy removal when dismantling is required.
Many MRO workshops have found repairs taking as little as half the time, thanks to fast cure times which make it quicker to get the repaired pump onto the test bench [see Case Study below]. Application is also easier, as LOCTITE® 518 is a single-component adhesive, which means it can be applied quickly with simply a gun or brush, after the parts have been cleaned with LOCTITE 7063 general purpose parts cleaner.
And to remove the cured product at the next service, all that’s needed is to spray the surface with LOCTITE 7200 cleaner.
Costing less than the traditional cut gasket or other, slow-curing, chemical solutions, the adhesive can be used on all types of pumps – from centrifugal to submersible, and from diaphragm and disc to double-jacket.
In line for less maintenance
A liquid adhesive can help solve another common cause of pump problems: shaft misalignment. Typically leading to premature bearing failure, the issue can be overcome with LOCTITE 290 medium-strength thread-locking adhesive.
The liquid adhesive fills the airspace and unifies the assemblies, which not only helps to resist vibration resulting from misalignment, but also shock, expansion and contraction. The clamp load is maintained and bolts are prevented from loosening, which helps in turn to maintain shaft alignment.
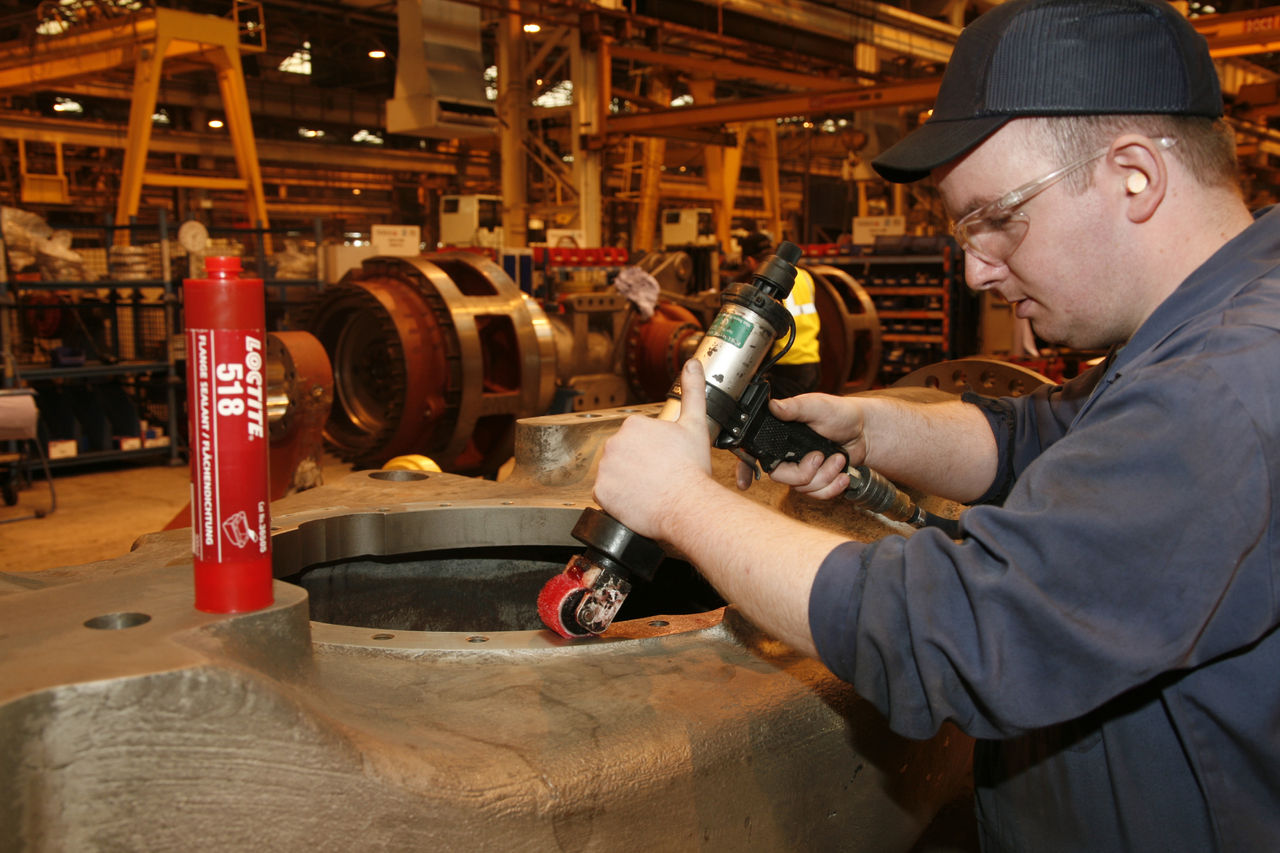
An industrial maintenance engineering services facility was dealing with repeated shaft misalignment and failures, on a customer’s centrifugal pump supplying water to a boiler in a commercial building. After cleaning the associated nuts and bolts with LOCTITE SF7603, and aligning the shaft of the motor and pump with a laser, the maintenance specialist applied LOCTITE 290 to the threads before tightening to the correct torque.
The result has been to eliminate misalignment issues between scheduled maintenance services, which take place only once every three years.
More solutions for less maintenance
Pump maintenance is crucial, but also time-consuming, inconvenient and costly. However, innovative and proven adhesive and sealant products such as the LOCTITE range can increase MTBF and shorten maintenance procedures.
With solutions to prevent bearings from fretting or spinning on their shafts or within housings, others to help prevent corrosion or chemical attack, and – of course – liquid gasketing adhesives, pump maintenance can be optimised, machine uptime maximised, and downtime and lost production minimised.
In fact, there are so many LOCTITE products available to improve pump reliability, it needs a poster to show them all. Download your free copy [link], or order from your usual ERIKS contact. And if pump efficiency is a sticking point, stick the poster where you’ll be sure you can’t miss it.
Manufacturing under pressure
A manufacturer of cast iron gearboxes and geared motors was using liquid gasketing on an adapter assembly flange. However, the product in question had two significant disadvantages. Firstly, its slow cure delayed production and testing. And secondly, even after testing, the final seal was poor – resulting in a leakage rate of 5%.
The manufacturer trialled a number of brands, before opting for a LOCTITE gasket sealant which met all their criteria.
Effectively filling all the gaps between the flange surfaces, the LOCTITE sealant cures quickly, allowing close-fitting parts to be instantly pressure-tested to 276kPa (40 psi). Not only have leaks been eliminated, but disassembly is also now far easier.
For more information on Maintenance Solutions and to get in touch with one of our ERIKS Specialists, please contact your local ERIKS Service Centre, who will be happy to discuss your options.
#Loctite #ERIKS #LetsMakeIndustryWorkBetter #AssetMaintenance #Pumps #Gaskets #Solutions