In this article
Sticking together through challenging times
The U.K. economy isn’t in recession. Is that how it feels to you? Thought not. So if, like many businesses, you’re still working hard to overcome rising energy costs, supply chain disruption, changing consumer demands and increased competition, stick around and keep reading.
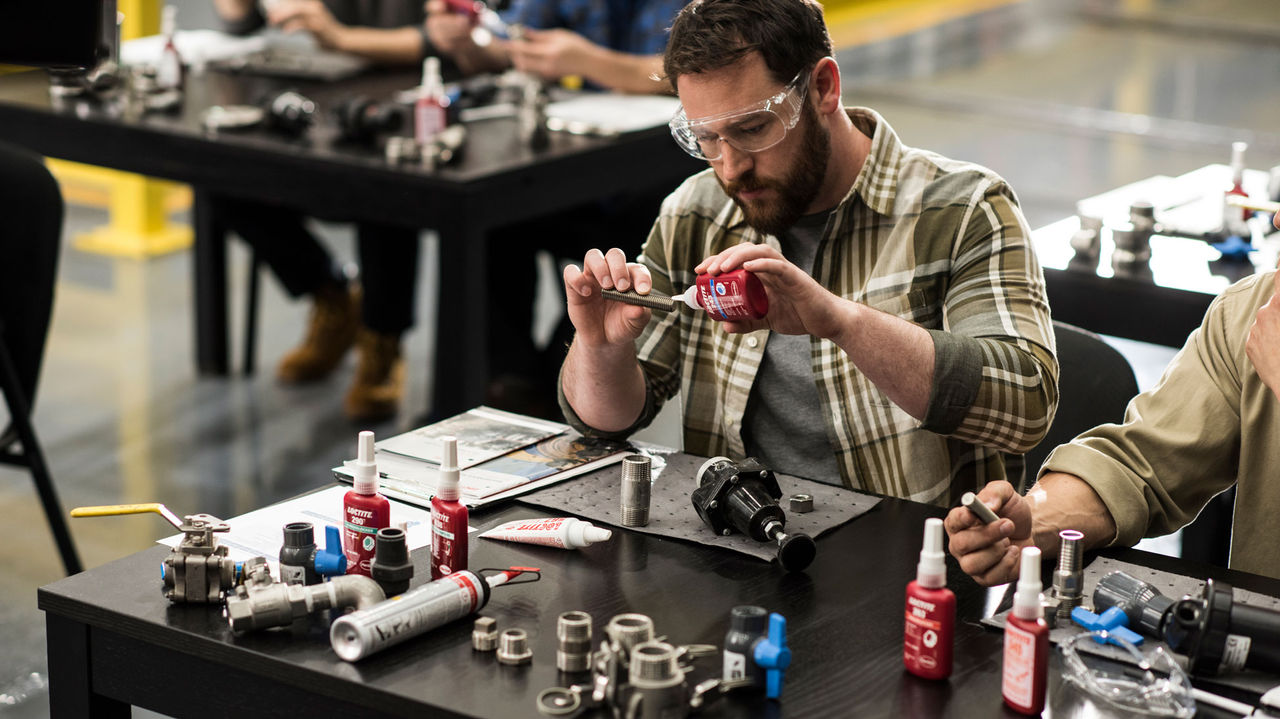
When you are striving to achieve a balance between cost reduction and quality assurance, there’s one set of substances that’s always a reliable choice. Adhesives and sealants are not always the first thought, but our customers are often surprised by just how valuable a solution they can be.
For example, there is a huge variety of tasks that can be improved by using structural adhesives.
From train carriage construction to recreational vehicles, and lift doors to electric motors, a vast swathe of manufacturing and industry relies on adhesives for structural integrity. And in maintenance, repair and overhaul applications (MRO), the right adhesive can make all the difference to a tricky repair: cutting costs and saving time, while still delivering a safe, secure bond.
Stuck where to start?
The sheer variety of tasks that can benefit from adhesives, and the sheer size of the LOCTITE range, can make it tough to know where to start. That’s why Henkel offers extensive support to manufacturers and MRO teams. Through dedicated survey and training services, we help businesses to make informed choices, to harness the innovation and agility that adhesives and sealants make possible – and ultimately to maintain their competitive edge.
Our detailed survey of your manufacturing plant and processes can identify potential cost-savings and improvements. It involves a tour of your production lines and sub-assembly areas, to document cost-reduction opportunities and potential challenges in MRO.
With the survey completed, a detailed audit of operations is provided, together with recommendations for process improvements, a report of cost-saving opportunities, and a cost analysis.
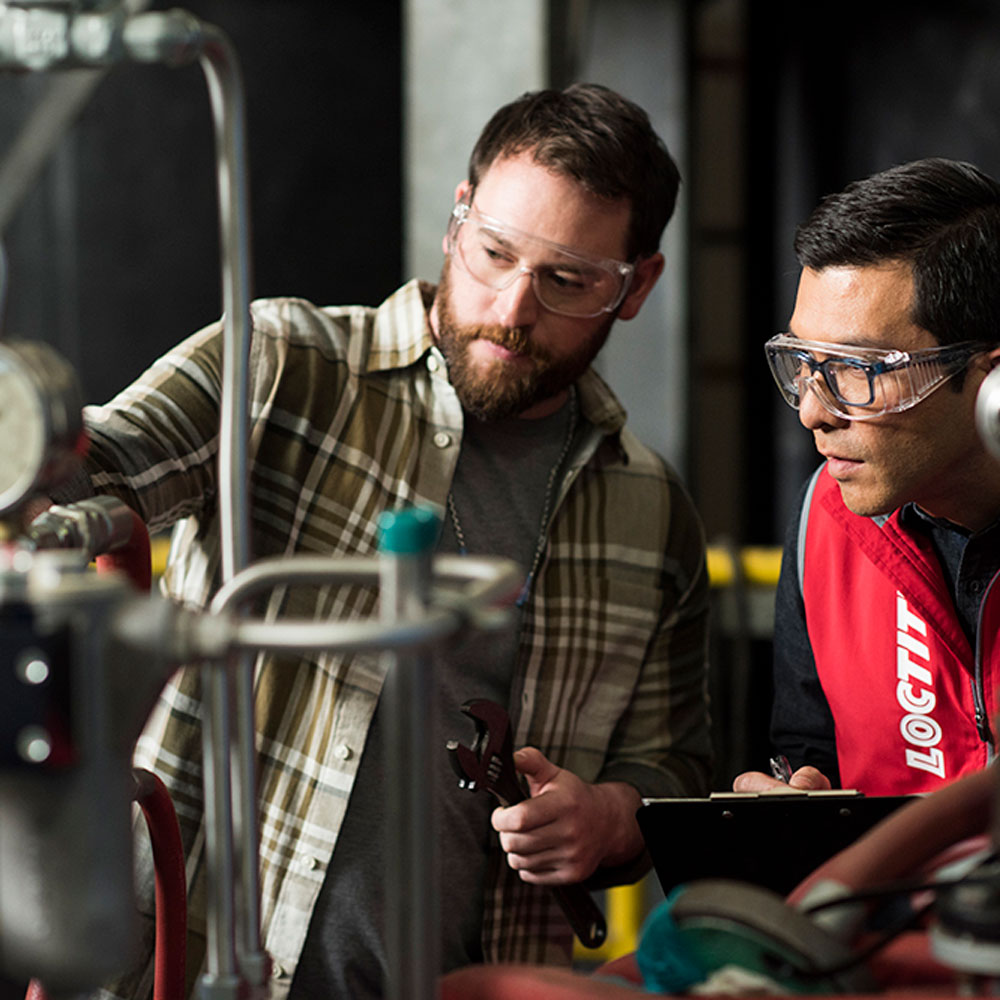
Using the findings, we can also deliver tailored seminars at your site, covering topics such as bonding, sealing, dispensing and curing equipment. The training incorporates technical guides, application information and case histories. Industry-specific application training helps manufacturers with selecting the proper adhesive and equipment for their assembly challenges, and attendees are encouraged to bring parts and specific design tasks to the workshop.
After an in-plant seminar, your teams will have all the knowledge they need for optimal application of adhesives and sealants: to increase process efficiency, reduce work in progress and manufacturing costs, improve throughput, increase quality and reliability, and automate previously manual processes.
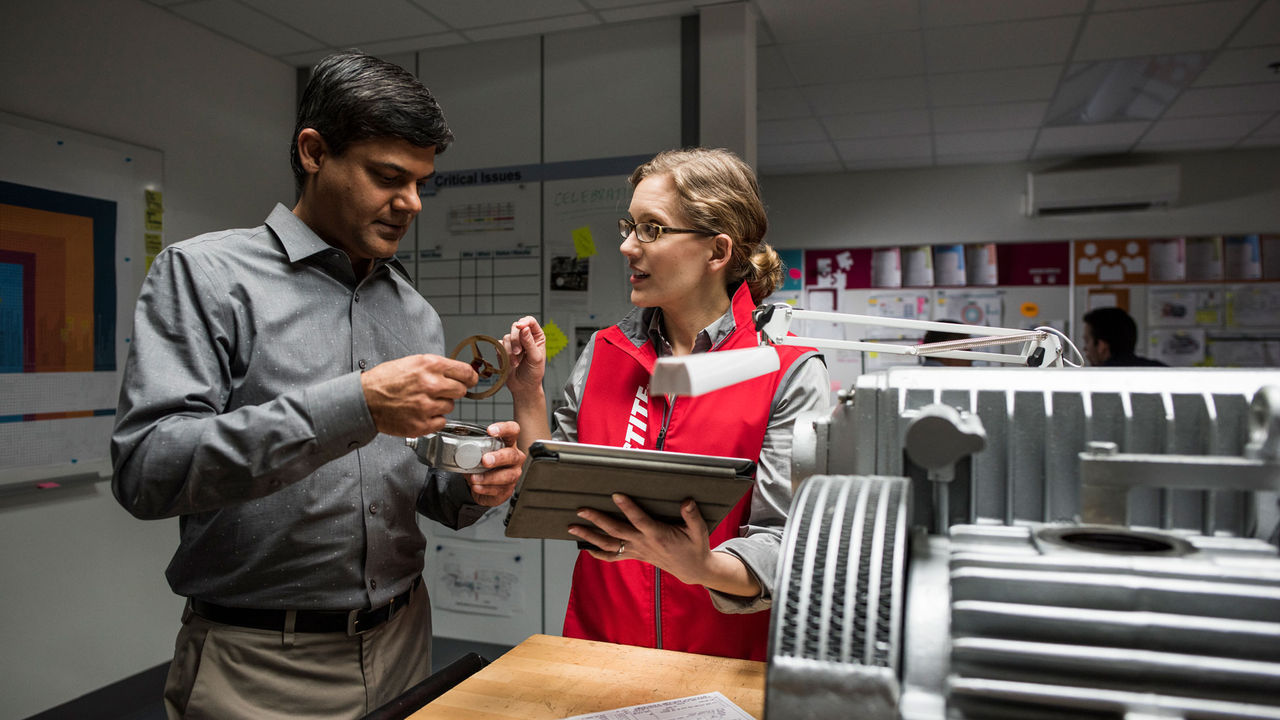
Stick with us
Our commitment is to be your true design partner, so LOCTITE seminars are just one aspect of the services and solutions we offer.
We aim to help your business to get the best from our solutions, whether you are creating a new assembly or enhancing an existing design. We work with you to develop and optimise adhesive, sealant and automation solutions to your specific needs – so you can reduce costs and improve reliability.
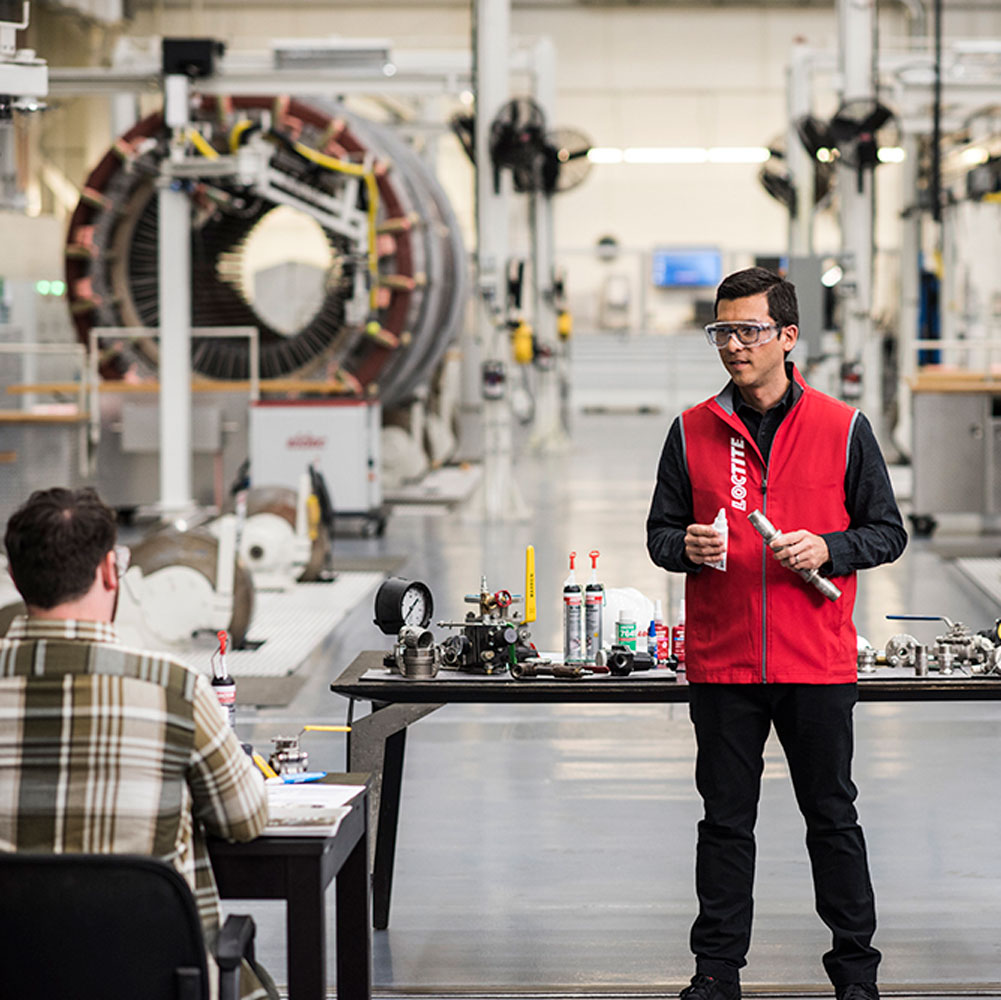
We understand that – recession or no recession – you face a multitude of challenges. But whatever the future holds for the economy, we are here to help you balance profitability and performance. Our products are designed to create a lasting bond, and we’re here to stick with you through even the toughest times.
LOCTITE in action
When a manufacturer needed to repair a shaft on a large fan that had been damaged by a loose, spinning bearing, the original solution was hardfacing and machining the shaft. This required five days of downtime and carried the risk of distorting and weakening the shaft. There was also no guarantee that the machining would prevent future fretting corrosion to the bearing fit.
After an assessment, the LOCTITE Engineering Solutions Expert provided training on a new repair method using LOCTITE products.
The main bearing was cleaned and removed, then before the bearing was slipped into the correct position, LOCTITE 638 Retaining Compound was applied to the shaft. This compound fills voids to prevent fretting corrosion and ensure even distribution of high load stress.
The whole operation was easily performed by maintenance personnel, and the fan was up and running in just 8 hours. The LOCTITE solution also prevented future damage to the shaft and maintained the fit over the life of the bearing.
For more information, contact your local ERIKS Service Centre, who will be happy to discuss your options.
#Henkel #Loctite #ERIKS #LetsMakeIndustryWorkBetter #CostSavings #Adhesives #Training #Survey